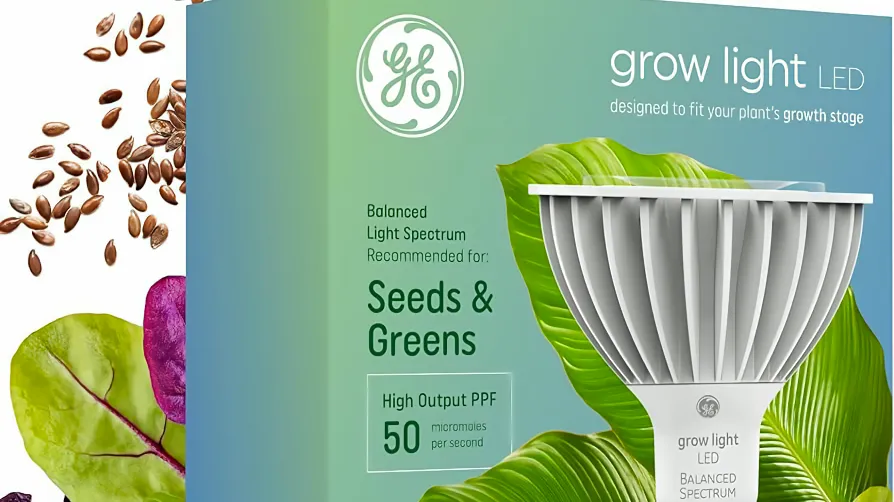
Industry:
Lighting Manufacturing
The Client:
GE Lighting manufacturer, Oakville Plant
GE Lighting Cuts $200,000 in Costs Through 360’s Energy Coach Program
GE’s Oakville lighting plant transformed from having an unfocused list of efficiency improvements to becoming a division leader in energy reduction, achieving over $200,000 in annual savings through a comprehensive approach that combined employee engagement, systematic procedures, and capital projects.
The Challenges
GE’s lighting plant had identified multiple efficiency opportunities through their Treasure Hunt program but struggled with prioritization and implementation. They needed to transform a simple list of potential improvements into an actionable, sustainable energy management strategy that would engage their entire team.
The 360 Solution
- Energy Team & Training: Formulated an Energy Team and attended the Sustainable Energy Plan workshop.
- Employee Engagement: Launched awareness programs with team competitions and point systems
- Targeted Time Periods: Focused on rest periods, evenings, and weekends for energy savings.
- Daily Energy Reports: Used reports to track hourly improvements, achieving a 45% reduction in non-production periods.
- Capital Projects: Undertook various projects, including heat recovery, boiler replacement, and compressed air isolation.
- Incentive Coordination: Worked with local utilities to apply for incentives, leading to annual savings of over $200,000.
The Results
- Cost Savings: Achieved annual savings of over $200,000.
- Employee Engagement: Over 400 energy savings kits delivered to employees, fostering a culture of energy awareness.
- Recognition: Became a premier site within division for energy initiatives
- Utility Partnerships: Secured incentives from Oakville Hydro and Union Gas
- Cultural Change: Created sustainable energy management practices throughout organization
- Project Pipeline: Established $300,000 in planned improvements for 2008
As General Electric carried out their yearly Treasure Hunt for efficiency measures, the lighting plant in Oakville was left with a laundry list of items to pursue for efficiency improvements. However, they did not have an action plan on how to tackle these items.
With the formulation of their Energy Team, they attended the Sustainable Energy Plan training workshop to get started. They quickly learned how to identify possible savings without capital investment. They targeted rest periods, evenings and weekends. They began using their daily energy reports to track improvements in their hourly profile. A 45% reduction in non-production periods was achieved in 2007. Plant shut down procedures have been written and measured to ensure this process continues and the low hanging fruit does not grow back. This site is seen as one of the premier sites in their division for energy reduction initiatives!
In addition, awareness programs were launched by formulating teams for each process line. The various teams then designed their own shut down procedures and checklists and had points allocated to each item. The shut down practices were monitored by energy alarming and team points were displayed on the plant’s energy board. At the same time, the site began tackling capital projects. Improvements included the make up air system, heat recovery from various pump rooms, a boiler replacement, compressed air isolation valves, spot cooling elimination, variable speed drives, elimination of all air vibrators, and a gas monitoring project for a real time system. All these projects were coordinated with the local utilities for incentive applications from Oakville Hydro and Union Gas.
A project template has been developed to help clearly define the projects and supply the utility with information ahead of time to schedule any applicable incentive program. All the projects have led to annual savings of over $200,000. For their efforts, the plant was rewarded with energy savings kits for their homes. The Energy Coach and Union Gas coordinated the delivery of over 400 savings kits to the plant and launched an employee appreciation event thanking the staff for their hard work over the year. With materials to save over $150 on their annual gas and water bill, the employees were more than happy to participate. The launch included an energy board with plant statistics on energy savings and awareness pieces. Projects in 2008 are estimated to be in the $300,000 range.
“The Energy Coach Program guides us, helping us to develop and then follow a detailed step-by-step roadmap to saving energy dollars. The assistance available to me includes idea generation as well as practical solutions tailored to my own situation.”