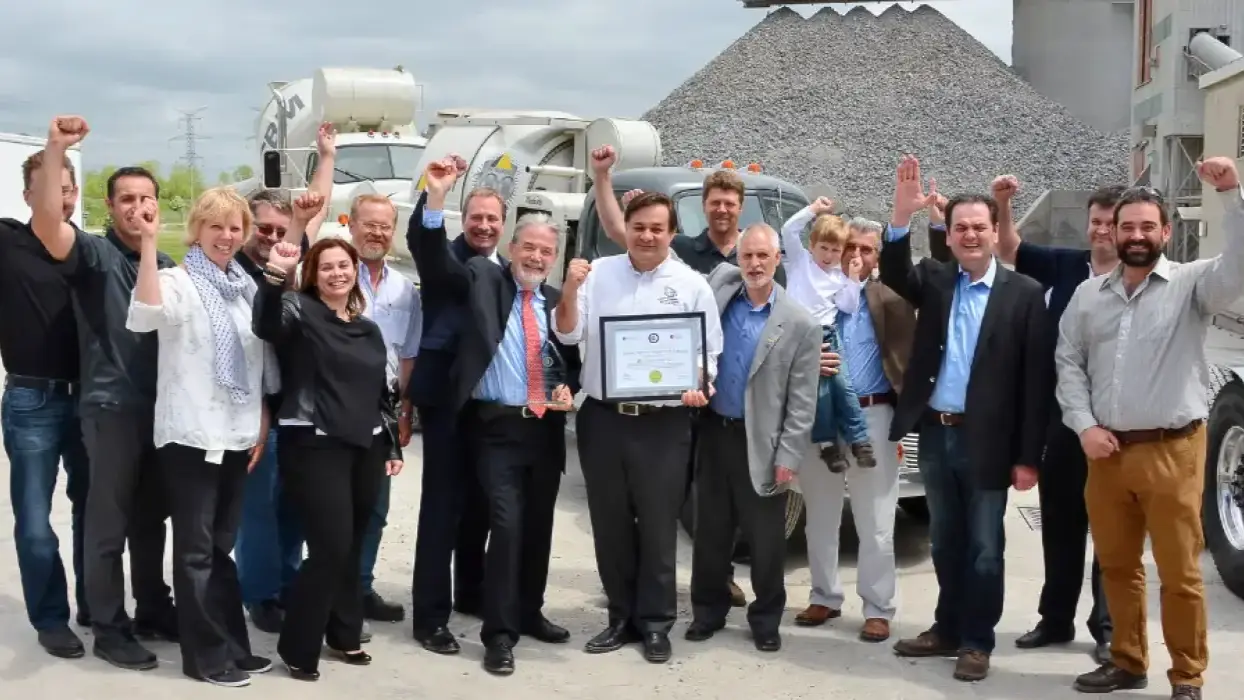
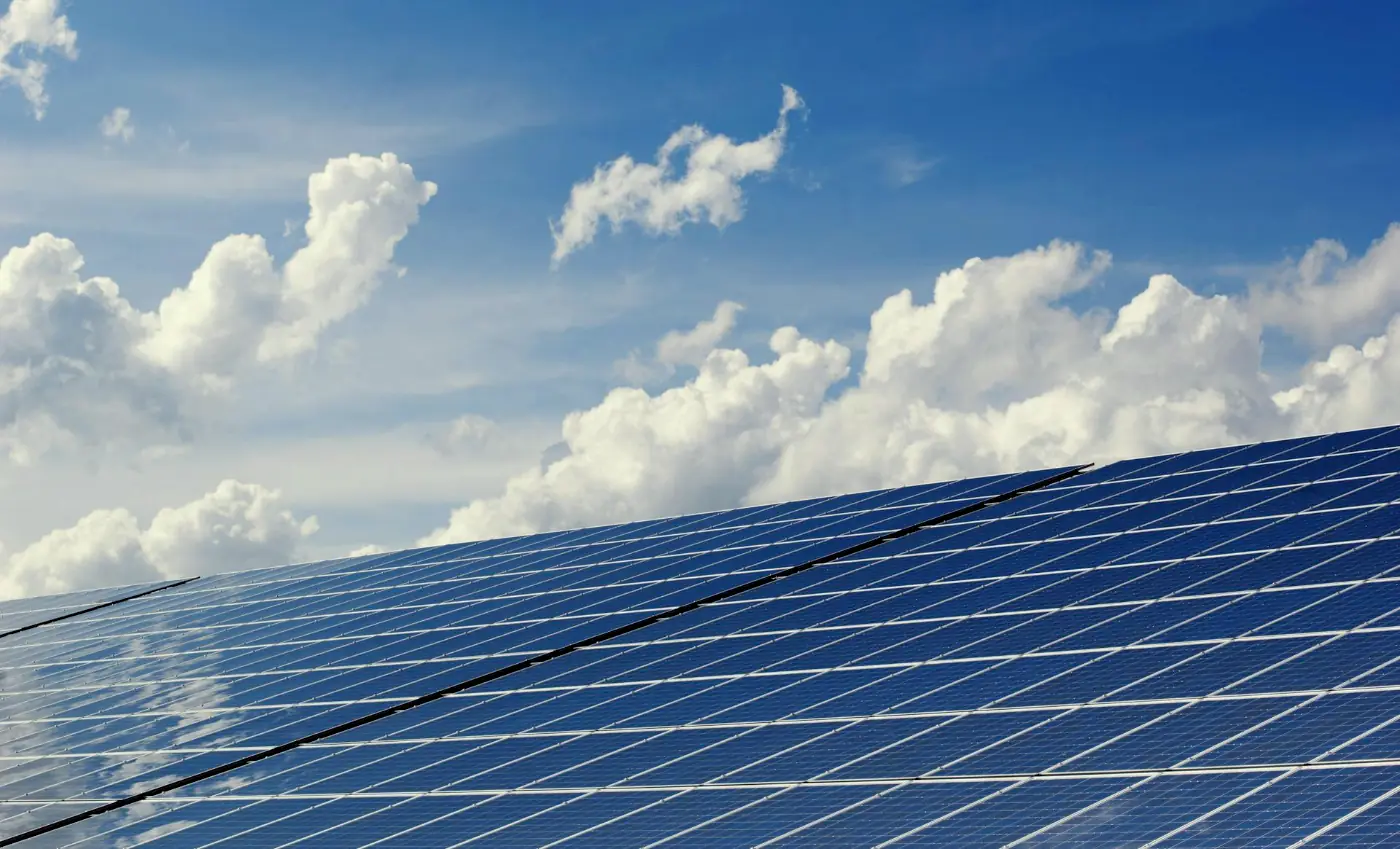
Energy Management
Energy Efficiency & Optimization
The energy team at Samuel, Son and Company’s plant in Fort Mill, South Carolina are successfully challenging an assumption that significant energy efficiency improvements can only be made using new technology. Tony Godbolt, Lauren Sanders, Butch Freeman, Jon Bryan and John Dimoff are proving that smart plant operators can make big energy savings without large capital investments.
The Fort Mill plant extrudes PET (Polyethylene terephthalate plastics), an energy intensive process. The energy team has been in place for eighteen months.
“We mapped each step in our PET manufacturing process to understand the energy consumption at each point”, says Jon Bryan, Senior Engineer at the site. “By understanding the flow of energy as it followed the production process, we figured out how to decrease electrical consumption. In some places, we were able to displace electricity with the less expensive use of natural gas.”
Optimizing energy use at each step in the process had a cascading effect – reduction at one step modified energy use at the next. The team was able to flatten the heat profile to ensure similar temperatures between consecutive steps in the orientation process. Raising the gas dryer temperatures, for example, reduced the load of a primary motor. Elevating certain water temperature set points avoided other operating costs. The net result was to lower the overall electricity draw within the plant.
Simple maintenance has provided the Fort Mill plant with other savings. Removing oil buildup from the cooling coils in one chiller dropped energy consumption by 40%. This pilot project was so successful, there are plans to extend it to other chillers in the system in 2020. Avoiding the replacement of capital equipment allows the plant to produce the same product, with minimal investment and lower cost.
Taken together, all these steps have meant big savings at Fort Mill site. “In 2019, our costs will be about $76,000 lower than they otherwise would have been,” says John Dimoff, Plant Engineer.
Fort Mill has additional energy efficiency projects under way. Providing outside air circulation to naturally cool compressor rooms is one of them. The savings have not yet been verified and reported. The team is investing in portable power meters to better enable them to track savings.
Not only is the energy team at Samuel’s Fort Mill plant proving that energy efficiency is possible without investing in new technology. In fact, they are showing how a strong energy management process can result in reducing energy use while also postponing the need for capital investment.
Status:
Ready
OG Link:
https://360energy.net/samuel-energy-team-achieves-success/
Notes: