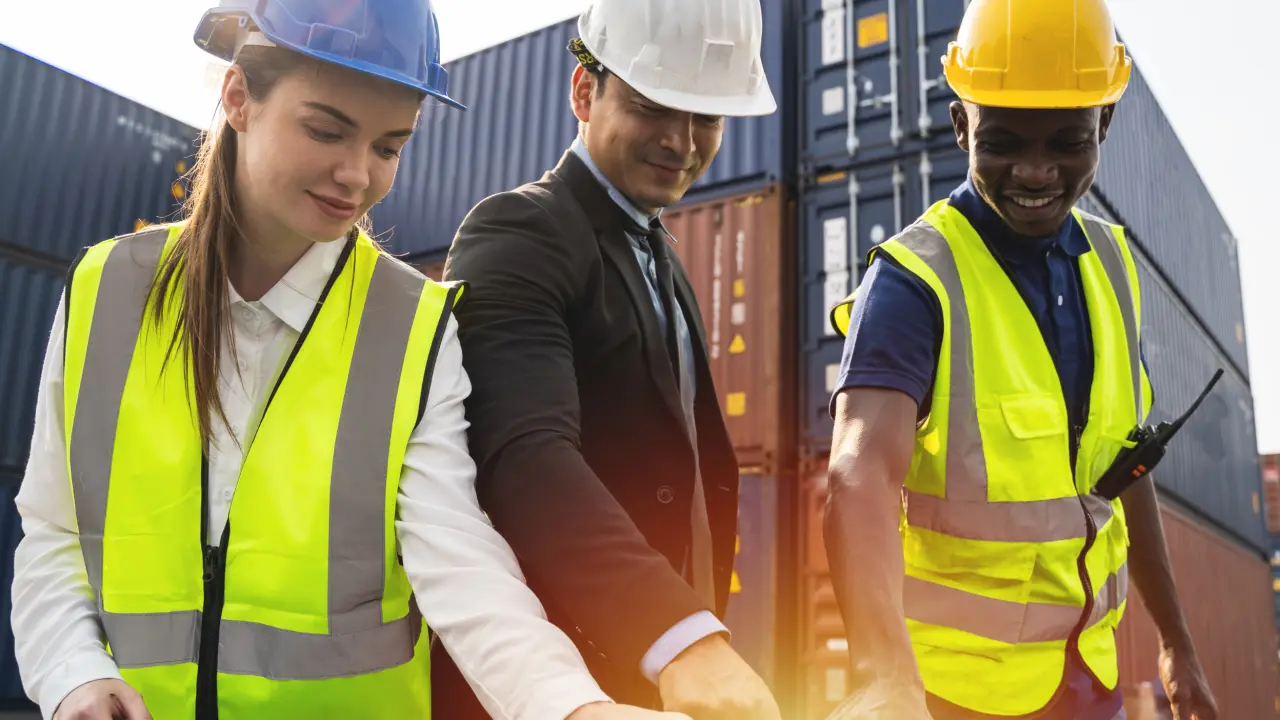
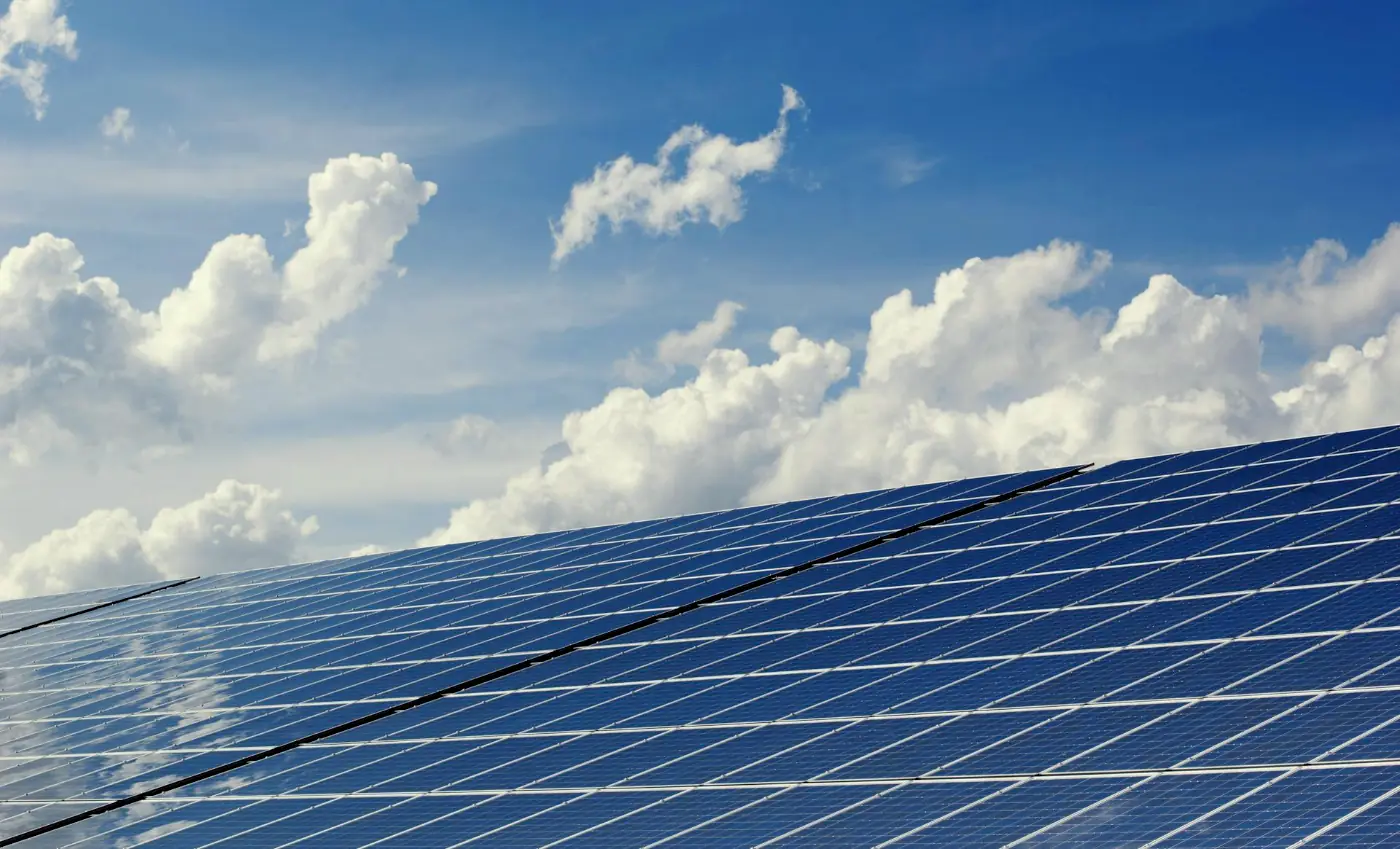
Energy Management
In 2006, St. Marys Cement in Bowmanville embarked on a Journey to Energy Excellence. Soon after they engaged 360 Energy to help guide and support them along the way. In 2014, Marty Fallon was the CEO of St. Marys Cement and was instrumental in fostering the energy management ethic at their Bowmanville site. That year, he spoke about his experience at CME’s Competitive Advantage Through Energy Conference in Mississauga, Ontario. For this week’s blog, we are sharing what he had to say about the St. Marys Journey to Energy Excellence.
I want to tell you the story of our Journey to Energy Excellence, why we started this journey, where it has taken us and what we have learned along the way.
My first observation is that we are still on our Journey to Energy Excellence. No matter how good we are or become, there is always room for improvement. We live in a competitive world. What makes us better one year needs to continuously improve to the advantage of our customers, our employees and our shareholders.
Let me set the stage by telling you a little about St Marys Cement at Bowmanville. St Marys is wholly owned by the Brazilian company, Votorantim Cimentos. The Division I lead produces cement, aggregate, and ready mix in multiple plants throughout North America. Our plant in Bowmanville is one of the largest of its kind in North America.
St Marys is like most manufacturers. We use a lot of energy to make our products. That makes energy critical to our competitiveness. Perhaps for us, it’s more so than others. As a company, we are always striving to reduce our energy and environmental footprint.
Energy is ⅓ of our cost of production. In our Bowmanville plant, we consume the same electricity as 25,000 homes and the same heat as 50,000 homes.
Our Journey to Energy Excellence began in 2006. The Canadian market was good, production was high, and profitability was meeting expectations. Some might have said it was an ideal time for our company.
We had a forward-looking team at Bowmanville led by the Production Manager, Fabio Garcia, and the Electrical Maintenance Manager, Jim Storey. Being good wasn’t good enough for them. They wanted their team to excel.
They knew that markets go through cycles and their Ontario plant needed to be ready for the risks of a slow market. To stay competitive, they knew they needed to look everywhere for cost savings and efficiencies. Then in 2008, the market disappeared. We lost 50% of our business almost overnight.
The first lesson we learned is that saving on energy falls right to the bottom line. Saving energy makes prudent business sense. Therefore, there is no better time than the present to begin looking for energy savings. Whether times are good for your firm or not so good, the time to start on energy improvements was “yesterday”. That’s how our Bowmanville plant led the way.
Before I tell you the rest of the story, let me tell you the outcome of our efforts. Our Journey to Energy Excellence has saved us $10 Million. And those savings just grow as each year goes by.
How did we begin? That is the second lesson we learned. To be effective, you will need to have a multiple approach concept. You will need everyone’s participation. We assembled our people from different areas and from different levels in the organization. We called our team E=MC². It stands for Energy Management Conservation Committee.
In large industrial facilities, it is the Facility Manager or Production Manager that has the most to gain if you can convince them to engage in the process. In our case, our managers were proactive and took the lead.
Getting a CEO to take the time is difficult at best. However, if someone has a good working relationship it helps in getting access to the CEO. That is an ideal starting place if you can do it. Getting the support of the CEO helps build and keep momentum.
Energy management should be everyone’s responsibility. If it remains the responsibility of one energy manager or one department, it can get isolated.
The third lesson we learned was that we needed a plan. We needed to rigorously review every department and section in our company to discover how we used energy, when we used it, and how we could use less of it, or use it more productively.
Many of you in the audience today are in middle management. Some of you are engineers and technical people. We discovered that we needed everyone’s insights to implement internal company projects to bring us these benefits. In our case, people with environmental or sustainability responsibilities helped identify our energy conservation measures.
Our employees did the heavy lifting at St Marys Bowmanville plant. In fact, they identified over 240 potential initiatives ranging from education to efficiency, financial to management actions.
By and large, these projects were not technology solutions. In fact, we spent very little capital – less than $100,000. For the accountants in the audience, an investment of that magnitude, with that kind of savings has an ROI of something like 1000% or more. You can see why I am sold on the value of energy management.
At the outset, we made good progress on our own. But we felt we had only scratched the surface; that we had just started down this road. We needed to verify that we had made progress. And we wanted to know how to get better. We needed coaching to get the best out of our team.
Then we were introduced to 360 Energy. They told us about the Journey to Energy Excellence and the certification process they use to ensure companies follow best practices.
This was the fourth lesson we learned. Excellence is a state of mind. It is a thought process. To achieve excellence, it has to become the culture of the organization. It needs to be embraced as a value for which everyone strives.
Our St Marys Statement of Excellence gives us a strong foundation. But we have to live those values every day for them to be real for our employees. The Journey to Energy Excellence reinforced our commitment to continuously improve in all that we do throughout our company.
A culture of striving for excellence is much different than a culture that tries to minimize mistakes. Many companies think that discovering their shortcomings is like admitting failure. At St Marys, we have learned that getting better only happens when we discover our shortcomings.
The last lesson I want to share with you today is to get a good coach. A good coach will sometimes bring up difficult truths. A good coach will often show you your shortcomings, then ask you to dig deeper. Growing better takes hard work. A good coach will prod you to do it.
Some companies may not have the culture and ability to learn with help from an outside advisor. But in our company, we recognize that we received valuable assistance at an important time.
Let me conclude my remarks this afternoon by telling you a bit about the Journey to Energy Excellence Certification process. I want you know why it has been very important to St Marys Cement.
People can tell you a lot of things. But it is only when they can point to an independent review, that you know their accomplishments are real.
This is the value we have received from the Certification Process. When I say we have saved $10 Million, it is confirmed by the National Energy Foundation in the United Kingdom. A referee from outside North America, who has no vested interest, has verified our results.
St Marys has received recognition from the media, from other manufacturers, from our peers in the construction materials industry, and from government. Our reputation was strengthened by having an independent verification of our accomplishments.
At St Marys, we are proud of our employees and all that we have accomplished at Bowmanville. Because of our success in our Ontario plant, we are taking the lessons we have learned to our operations elsewhere in North America.
Even our head office in Brazil has noticed our efforts. Brazil relies on hydro electric power and has a big energy problem right now because the rains didn’t come. They are interested in what we have learned here; because it does not matter where a company operates Energy saving initiatives allow a company to become more competitive.
In summary, here is what I want to leave with you today:
I believe that if you adopt these lessons in your organizations, you will make Ontario and Canada more competitive, productive, and economically stronger.
Thank you for your attention.
Status:
Ready
OG Link:
https://360energy.net/lessons-journey-ceo-speaks/
Notes:
Should the author be Marty Fallon?